(๐ผ๐จ ๐ฎ๐ค๐ช ๐ฌ๐๐ก๐ก ๐๐๐ฉ๐๐๐ง ๐๐ง๐ค๐ข ๐ง๐๐๐๐๐ฃ๐, ๐ฉ๐๐๐จ ๐ฅ๐ค๐จ๐ฉ ๐ฌ๐๐จ ๐ฌ๐ง๐๐ฉ๐ฉ๐๐ฃ ๐๐ฃ ๐ฟ๐๐๐๐ข๐๐๐ง ๐๐ช๐ฉ ๐๐ช๐ ๐ฉ๐ค ๐ค๐ช๐จ๐๐๐ ๐๐จ๐จ๐ช๐๐จ, ๐ฉ๐๐๐ง๐ ๐๐๐จ ๐๐๐๐ฃ ๐ ๐๐๐ก๐๐ฎ ๐๐ฃ ๐ฅ๐ค๐จ๐ฉ๐๐ฃ๐ ๐๐ฉ)
November / December 2022
Hi again everyone..
Progress has been made once again with my home build fixed wheel bike, and to be honest,
probably with a little less in the way of setbacks in this instalment.
Here goes..
You may remember, the next challenge was going to be brazing the rear triangle to the main
frame. This in itself, poses one or two problems, as I canโt apply too much heat to them as they are heat treated tubes. With this in mind, I needed to finish the bronze and latterly brass fillet brazing to the bottom bracket, which I had fashioned some homemade lugs to accommodate the chain stays (I needed to do this, as the chainstays are heat treated and I wanted them to get a good strong mount to the bottom bracket shell)
So with fillet brazed BB lugs in place, I was then able to install the heat treated tubing. This
time, sweating them in with silver solder, which in temperature terms, melts at a much lower
point than brass or bronze, but which also makes for some incredibly strong joints, especially
when used in a lugged construction.
I decided not to make a jig in the end to assist with the alignment, as I thought, being a one off, I should be able to get it pretty near?
Once the chainstays were in place, the bike would actually sit up and self support itself.
Suddenly the seemingly fragile tubing was taking on a new lease of life and showing signs of
being pretty strong construction. See photo, of the back end without seat stays added.
I then added the horizontal dropouts, applying small amounts of silver solder to tack into place and compare with my 1:1 plan.
After which I needed to install the seat stays. I held them in place, (you may remember, I want Helenic stays, which come past the seat tube and install onto the top tube. Purely from a cosmetic point of view on my part. GT Bikes often use this method)
I had made some prototype tubing ideas from Toilet roll tubes, as I want an inverted curve
silver soldering into the tube. Easier for you to see the photo than me to explain fully.
I set about cutting the seat stays to length, cut out the section from them and inverted it to
form the fluted effect, silver soldered in place and then to the frame. Already the silver solder
was doing a great job of holding everything together, and the rear triangle looks pretty good!
I canโt say it is fully true, but it looks not bad at all!
Once the rear triangle was in place, I spent the evening looking at the bike with a bit of
disbelief, knowing that I have built it. While currently waiting for some more silver solder, my
curiosity started to get the better of me.
โWould this bike, in its current stage, support my weight?โ
I waited until everyone was out and decided to prop myself up against the kitchen door frame
and gently lower myself to stand onto the cranks. (Seat not fastened yet!)
Believe it or not, it held my weight! Nothing snapped! Nothing groaned! (thankfully neither did
myself!) It just did what I hoped it would, and supported my not so lightweight stature!!
AMAZING!
Thank goodness for triangles..
Whether it will have this level of compliance on the road remains to be seen! But in the mean
time, it is looking promising. I still have no idea whether I will have a rideable bike at the end of
all this, but every hour I spend in construction is one hour nearer to finding out!
During this stage of the build, the fillet brazing around the bottom bracket and down tube and seat tube, was pretty poor to be fair, but on sourcing some thinner brass rods, the whole process become much more easier and I was soon able to tidy it up considerably!
The Americans have a phrase for brazing for when the braze forms nice overlapping pools whilst molten. โStacking Dimesโ Mine isnโt quite stacking dimes, but I can now see evidence of that in places. (Some builders would rather fillet braze and smooth it by careful application and grinding techniques in any case)
I have also found that when brazing goes right, much less gas is used in the process, as time is optimised much better. So.. why โBermuda Triangleโ
Well I was working on the rear triangle, and it was the most catchy title I could think of!
I am currently typing this blog, waiting for my Christmas cake to come out of the oven. Due
some time around about midnight. I hope you have enjoyed reading these blogs as much as I have reliving the processes I have encountered through the bike build.
The bike is now sat on wheels that I built in 2009 (a radial laced front, based on a DT Swiss 240 which spins forever. I have never trued this wheel since built, and the unusual green back wheel, which to me is more unusual not because of its colour, but because I built it with a 4 cross lacing, which I donโt think you see too often.
Anyway, the cake beckons my attention, see you soon when I hopefully get to the stage of first test drive, adding bottle bosses etc, prior to final colour choice and eventually painting.
Safe riding in the mean time!
Best Wishes..
Mark Brownless
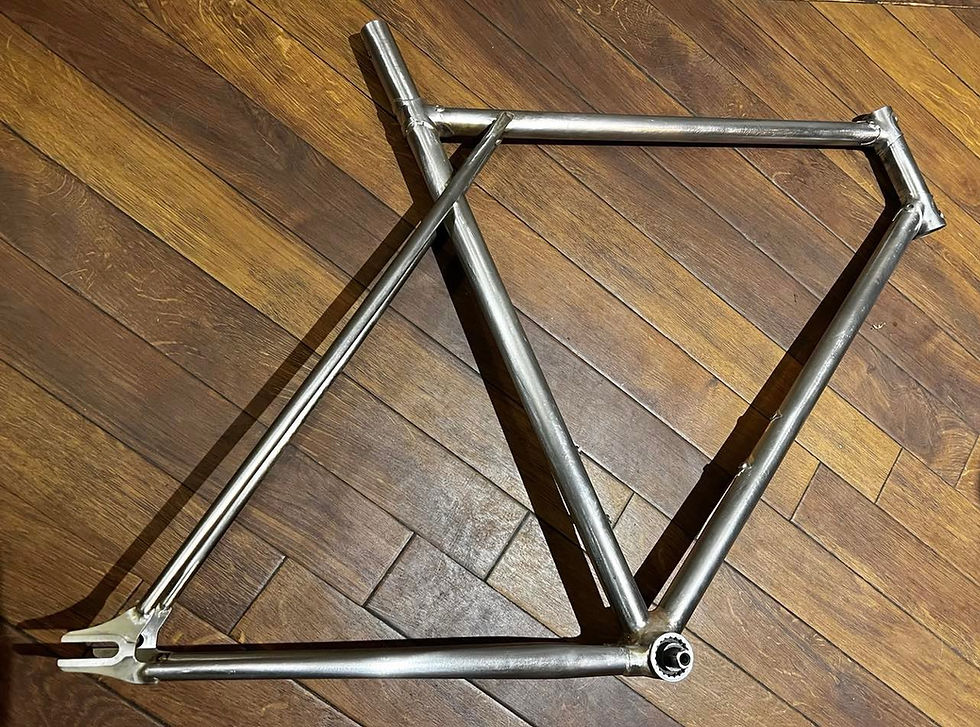





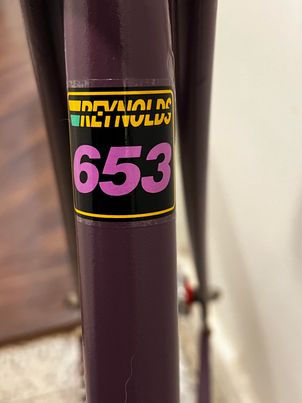
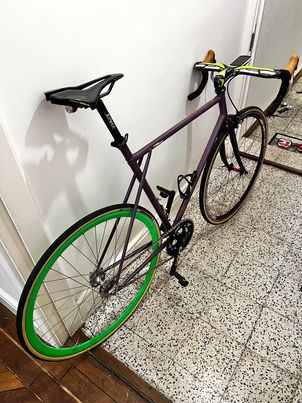
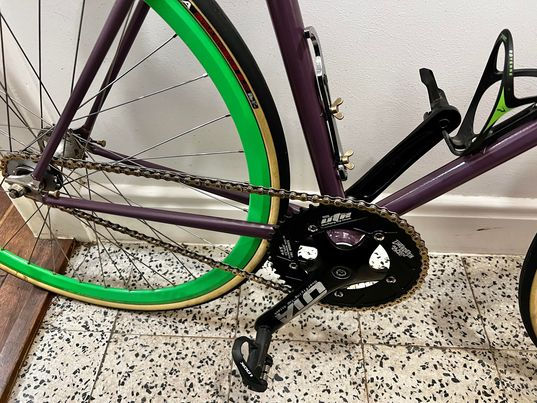

Mark
Hi Mike, well it just shows what is possible when you put your mind too it ! Well done... I built some cross 4 wheels in the past, took longer, they are a bit heavier but exceptionally strong... Great all seasons wheels